Pentatonic On the Road
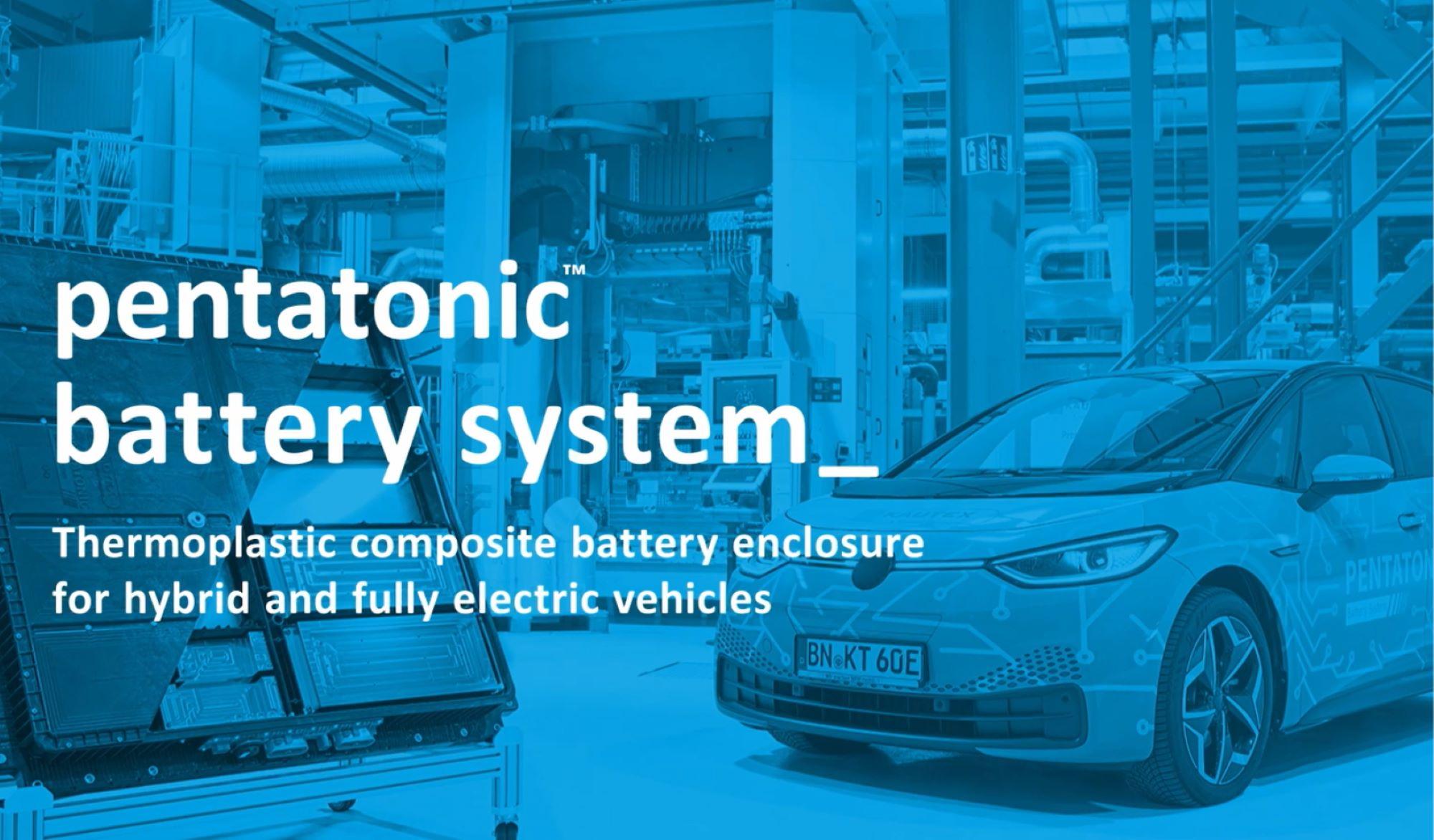
Versuchsfahrzeuge auf der Straße
Im Jahr 2021 haben wir ein Hybridfahrzeug in den USA gekauft und mit unserem Pentatonic Batteriegehäuse aus thermoplastischen Komposite ausgestattet. In kurzer Zeit haben wir damit über 50.000 km zurückgelegt und sind in den USA von Küste zu Küste gefahren.
Im Jahr 2022 haben wir ein rein elektrisches Fahrzeug in Deutschland gekauft und mit unserem Pentatonic Batteriegehäuse ausgerüstet. Zusätzlich haben wir das Pentatonic Batteriegehäuse mit Sensoren ausgestattet. Das TÜV-zertifizierte Fahrzeug mit Straßenzulassung haben wir auf der Rennstrecke und bei New Mobility Rallyes getestet und sind damit bereits über 8.400 km quer durch Deutschland gefahren.
Im Jahr 2023 haben wir unsere Flotte an Elektrofahrzeugen um ein weiteres rein elektrisches Fahrzeug erweitert, dieses Mal in den USA. Folgen Sie uns auf Instagram , um auf dem Laufenden zu bleiben!
Ein Produkt; drei Demonstratoren. Unsere, in drei Fahrzeugen installierten, Pentatonic Batteriegehäuse haben bereits mehr als 55.000 km zurückgelegt. Unser neuestes Versuchsfahrzeug verfügt über ein System, das auf unserer Formpresse in China hergestellt wurde, mit der wir eigene Tests und Bemusterungen für Kunden durchführen und bereit sind für die Serienproduktion.
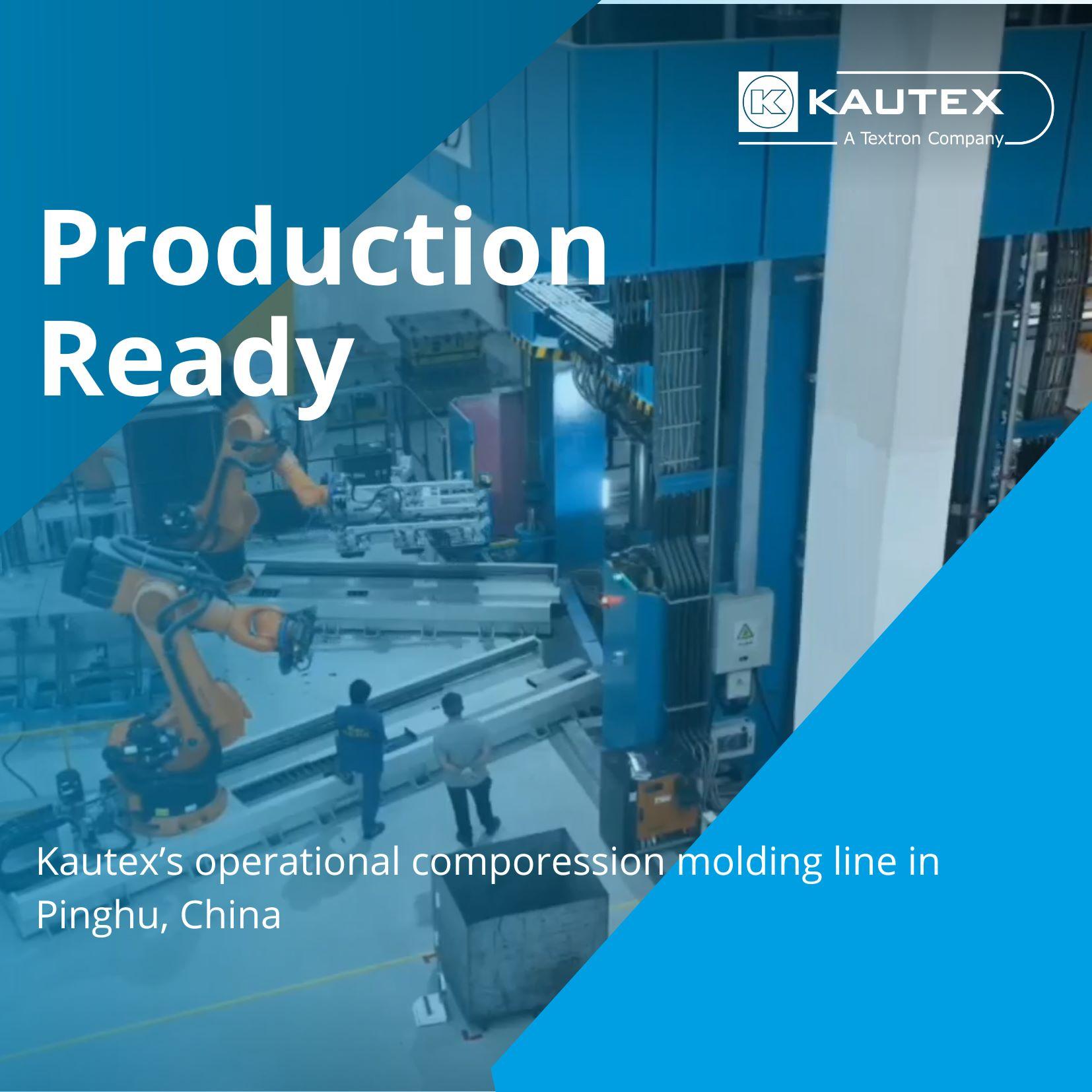
Bereit für die Serienproduktion
Auf der 2022 in Betrieb genommene Formpresse im chinesischen Pinghu wurden bereits Kundenversuche und Bemusterungen durchgeführt – und das Pentatonic Batteriegehäuse für das neuste Demonstrationsfahrzeug hergestellt.
Vorteile
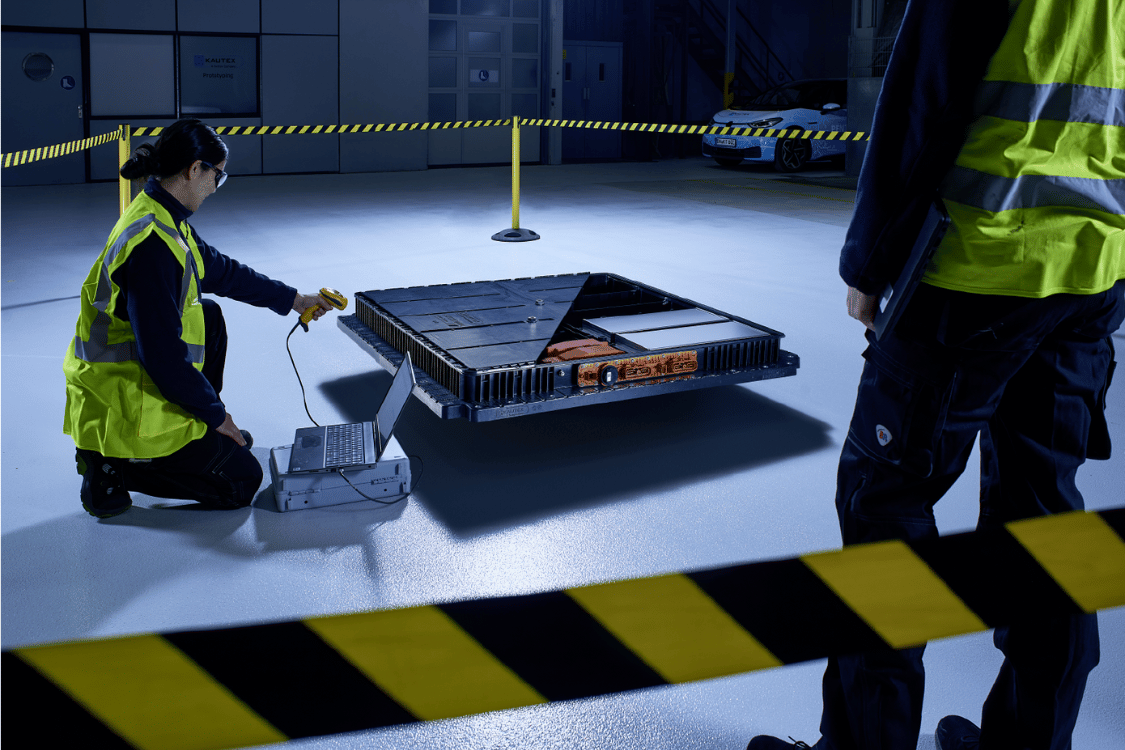
Sicherheit
Sicherheit in der Produktion und Anwendung haben für uns höchste Priorität. Durch unser nichtleitfähiges Gehäusematerial wird das Risiko eines Stromschlags gesenkt und Korrosion verhindert.
Funktionsintegration
Zusätzliche Funktionen und Komponenten wie Kühlplatten oder andere Kühlsysteme sind in ein leichtes und voll funktionsfähiges Batteriegehäuse integriert. Die Reduktion sekundärer Prozessschritte vereinfacht den Montageprozess, reduziert die Stückliste des Kunden und senkt die Kosten um bis zu 20 %. Weniger Montageschritte minimieren die Anzahl der Dichtfugen, was das Risiko für Undichtigkeiten verringert.
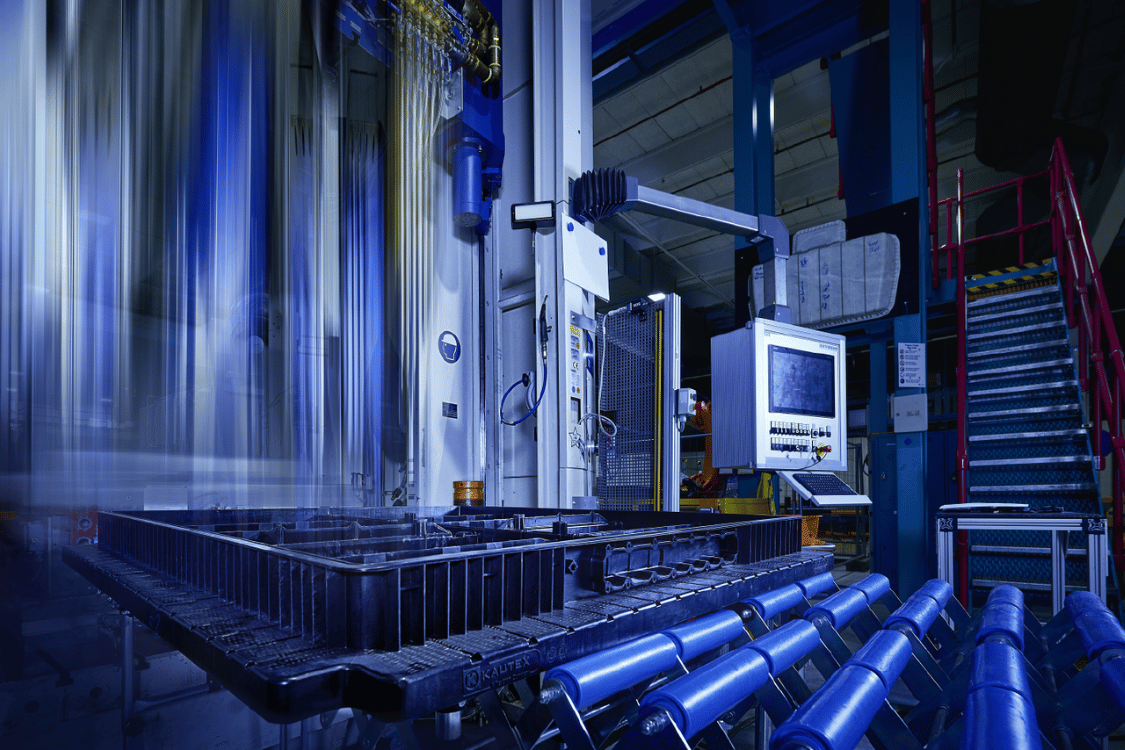
Fertigungsprozess
Durch unseren “One-shot”-Prozess können bereits im Fertigungsprozess vielfältige Funktionen integriert werden. Dadurch reduzieren sich sekundäre Prozessschritte, die Montage wird vereinfacht und die Dichtigkeit wird durch das wegfallen von Schweißungen verbessert.
Außerdem erfolgt die Integration von verstärkenden Strukturelementen direkt im Spritzguss- oder Formpress-Prozess.
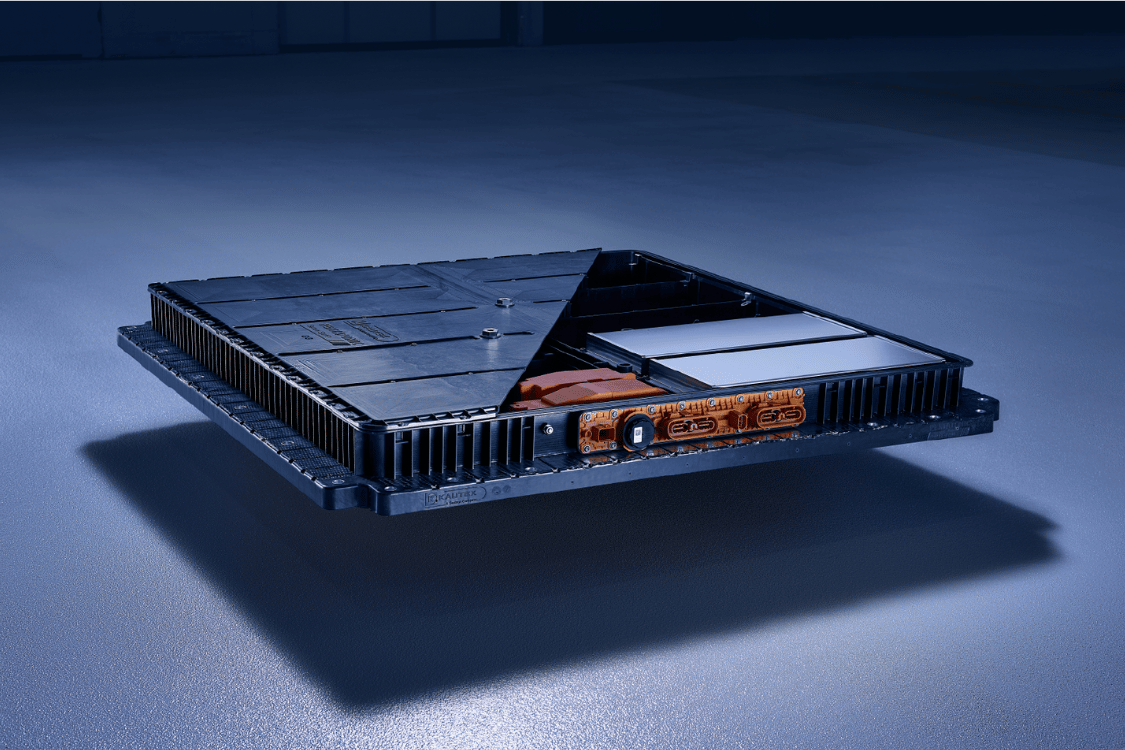
Gewicht
Das Pentatonic Batteriegehäuse wiegt bis zu 30 % weniger als ein vergleichbares System aus Stahl oder Aluminium. Dadurch wird die Reichweite des Fahrzeugs verbessert und Möglichkeit geschaffen Karosseriekomponenten anzupassen.
Unser Pentatonic Batteriegehäuse ermöglicht die Erhöhung der Nutzlastkapazität bei gleichzeitiger Senkung der CO2-Emissionen und des Energieverbrauchs im Fahrzeug und entlang der Lieferkette.
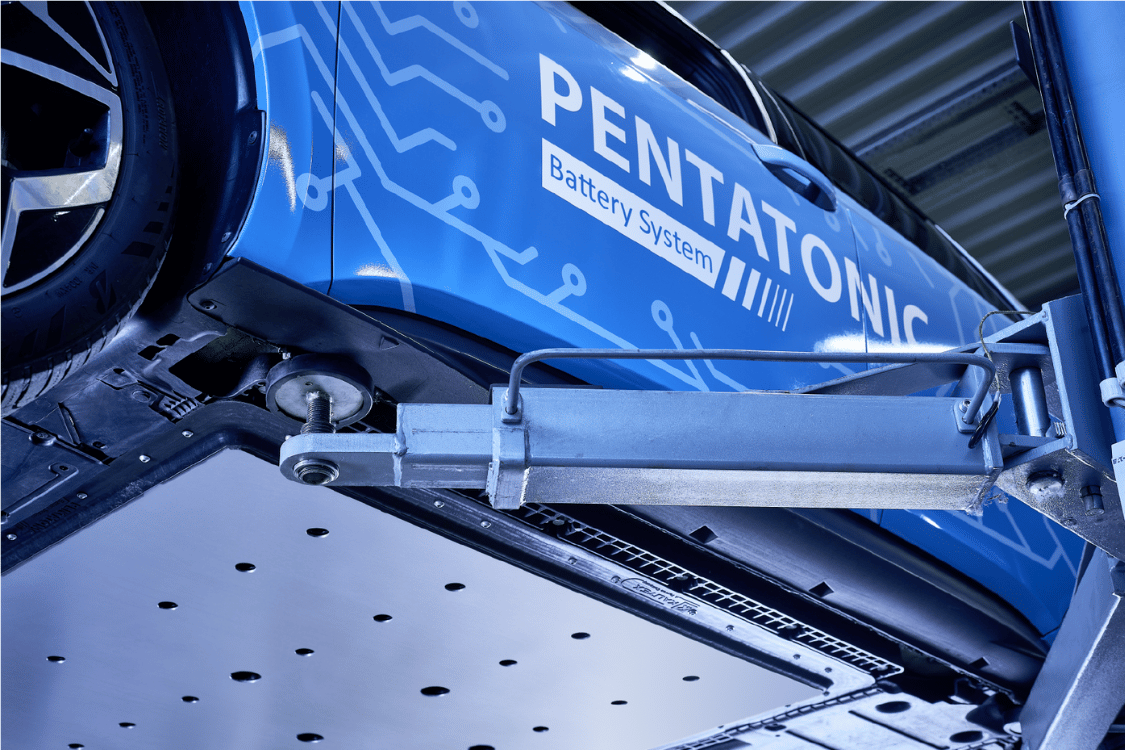
Volumenvorteile
Aufgrund von hervorragenden Isoliereigenschaften unseres Materials und einem höheren Grad der Integration von zum Beispiel Kühlplatten, kann der Abstand zwischen dem Pentatonic-Gehäuse und den Modulen oder Batteriezellen im Vergleich zu herkömmlichen Gehäusen reduziert werden. Hierdurch ensteht in dem gleichen Bauraum mehr Platz für die Module oder Batteriezellen.
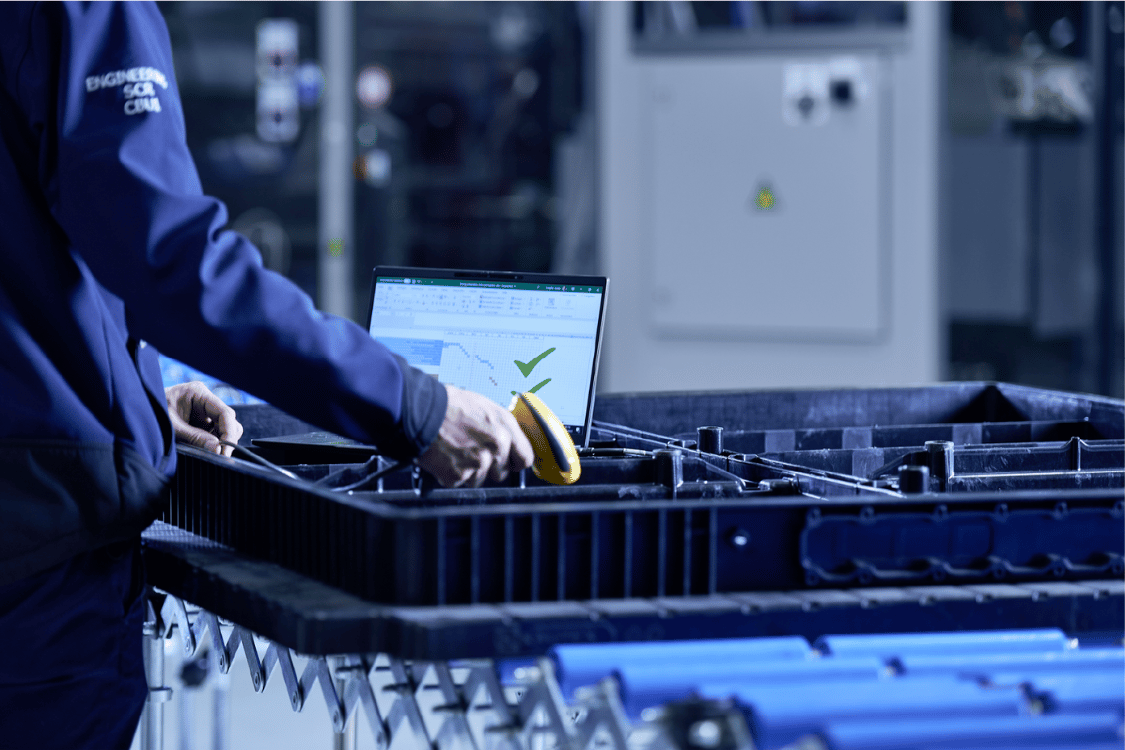
Homologation
Als Pioniere in der Produktion von Kraftstofftanks aus Kunststoff haben wir jahrzehntelange Erfahrung mit Brandtests, Dichtheitsprüfungen und Crashtests. Diese Erfahrung nutzen und erweitern wir, um die Anforderungen eines Batteriesystems, z.B. nach ECE R100 oder GB38031-2020, sowohl für das Design als auch in der Herstellung zu erfüllen.